by Lean Six Team | Dec 26, 2024 | Education
One of the most frequently asked questions we get at Utah Lean Six Sigma Training Center is: How does Lean Six Sigma work? At first glance, Lean Six Sigma might seem like a complex, almost mystical body of knowledge—something that requires years of study under a seasoned expert. But in reality, the principles of Lean Six Sigma are straightforward and practical, and their effectiveness lies in applying them to real-life scenarios.
What Lean Six Sigma Really Is
Lean Six Sigma is essentially a toolkit—a collection of knowledge, skills, and abilities that help you analyze and improve processes. Just like mechanical engineering allows someone to design and optimize physical systems, Lean Six Sigma allows you to look at a process and ask: What’s working? What’s not? Which parts are causing inefficiencies or delivering poor results? The end goal is to create processes that deliver results consistently, in ways that meet or exceed customer expectations.
This toolkit isn’t about learning in a vacuum. In fact, the majority of learning happens by doing. In Lean Six Sigma, less than 10% of learning is from traditional classroom settings—the rest comes from practicing, applying, and solving real-world problems. So, if Lean Six Sigma sounds intimidating, remember: it’s meant to be used, tested, and adapted on the job.
Analyzing and Improving Processes
Lean Six Sigma equips you with the tools to analyze processes. You learn to understand which parts are working, which parts are “in control,” and which parts are consistently failing to deliver the expected outcomes. Imagine you’re looking at a factory assembly line, a customer service response chain, or a software deployment process. Lean Six Sigma helps you identify what’s going wrong—what’s generating those “bad outputs”—and, more importantly, which aspects of the process are impacting your customers negatively.
After analyzing the process, Lean Six Sigma provides a wealth of methods to help fix it. Spoiler alert: it’s rarely just one thing that’s causing an issue. Lean Six Sigma guides you through identifying, fixing, and then controlling those problems, so they don’t come back. It’s about understanding that processes can always be improved, often in more than one way, and then maintaining those improvements for long-term benefits.
Making Lean Six Sigma Work for You
The magic of Lean Six Sigma isn’t about the terminology or the idea of becoming a “belt” of some sort—it’s about gaining the skills you need to make processes better. Whether that means reducing waste, increasing quality, speeding up service, or simply getting consistent results, Lean Six Sigma is about providing the practical tools to do so.
At Utah Lean Six Sigma Training Center, our mission is to keep it practical and effective. We understand that learning happens best when you’re actively involved in improving processes, not just hearing about them in theory. That’s why we encourage questions, interaction, and real-world practice—we’re here to help guide you through every step of the journey. No high-pressure sales tactics, just honest help to make sure you succeed.
If you have more questions about Lean Six Sigma—how it works, what it can do for you, or where to start—don’t hesitate to reach out. We’re here to support you on your continuous improvement journey. Let’s turn your interest into tangible skills that can transform your business and career.
by Craig Johnson | Feb 24, 2022 | Education
Tell me if you’ve heard this Lean joke before: A husband and wife walk into a bar the store…
The Setup
Two weeks prior, they had ordered a series of frames for new family photos to adorn their living room wall. They sat with the salesperson, weighed the options, paid a deposit, and left with an eagerness for the joy the images of their beloved family would add to their home. The photos would be particularly nice for the upcoming family summer party they were hosting in the very near future.
The couple waited patiently for those two weeks to pass. During this period of patient anticipation, they prepared the wall by removing the old photos and adding a touch of new paint. They measured and located where each hook would be placed.
The Crisis
Finally after the two weeks of waiting they excitedly drove back to the store to pick up their promised framed photos. They walked to the will call window, presented their receipt, paid the remainder of their bill…
And were told their frames weren’t ready.
The Fake Victory
Exasperated, the now-frustrated couple inquired as to why their frames weren’t ready. A litany of excuses were offered, followed by many apologies, followed by zero excuses. The proverbial ball had simply been dropped.
In a blur of activity, store workers swarmed like the bees in a disturbed hive. One ran to the back room to pull inventory. Another dashed across the showroom to pick up the prints from their storage room. Yet another busy bee disappeared behind a desk to make a series of phone calls, pulling more resources in. At the end of a very hectic 15 minutes the workers proudly presented the couple with their freshly packaged set of framed family photos.
The False Thrill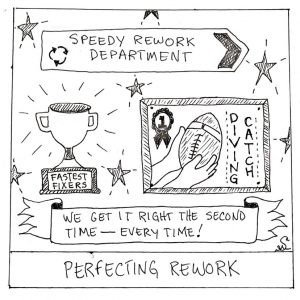
As the husband and wife left, the workers held a mild celebration. As a result of the (fake) victory, backs were patted. Cheers were raised. Fives were… highed. (Please forgive the author for that last one)
Once the excitement of spontaneous teamwork and the thrill of overcoming this hurdle subsided, work went back to normal. For months, workers fondly recounted stories of “that time we all came together”. Company leaders spoke about it at annual meetings.
Taking off the Rose Colored Glasses – A Lean Perspective
To be fair, using shared trials is a great way to build teamwork. There are, however, better ways to do this. Chief among those better ways are those that don’t include an unhappy customer. The first principle of Lean is to identify value. This means we understand exactly what our customers want and then spend the rest of our efforts in meeting those customer requirements.
The reality is that even though the team pulled together to get the order done, the victory was false – diminished value was provided to the customer. Yes, the customers got their frames, but as Taguchi taught us, anything that deviates from perfect is a loss of value. These customers got their frames – but they got them late. The company got paid, but what are the chances those customers return again? What are the chances they tell their friends and relatives about their negative experience? How much time did we spend responding to this self-inflicted emergency when we could have been doing value-added work? How much more of this chaos can our employees take before they seek greener, more peaceful and organized, pastures?
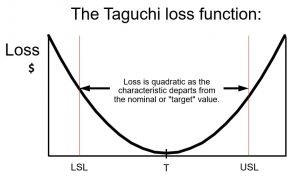
Click to Enlarge
See Defects as They Really Are
It does very little good for us to celebrate victory over our problems if we do nothing to learn from them and make sure they don’t happen again. When defects occur, recognize them for what they are: negative experiences that, although they can also be learning experiences, are nonetheless damaging to an organization. Defects should be investigated, analyzed, and eliminated. Controls should be put in place to ensure the defect doesn’t happen again. Basic Lean tools such as 5S, standard work, mistake proofing, and visual management should be implemented. For larger, more systemic problems, formal projects should be organized and given the support and resources needed for success. Lean practices, including those taught in the Utah Lean Six Sigma Training Center courses teach us to pursue problem solving and improvements with relentless determination.
What’s Better Than Fixing Problems?
Fixing a problem, especially when a team really comes together to do it, can be really rewarding. The far better, albeit potentially less exciting, option is making sure the problem doesn’t happen in the first place. In the Utah Lean Six Sigma Training Center Green Belt course, students learn to perform proactive problem solving. Students are taught to analyze a process to determine what could possibly go wrong, prioritize these failure modes, and then implement preventive measures to eliminate the threat of the defect occurring.
Get the Lean Training You Need
Utah Lean Six Sigma Training Center works hard to bring Lean training to Utah that is applicable, attainable, available, and affordable. We stand ready to meet your needs. To help you make the best choice possible when choosing a training provider, we’ve written an ebook to help walk you through a complex decision. Get your free copy here.
See you in class!
by Craig Johnson | Aug 17, 2021 | Education
Click on the images to learn more about Utah Lean Six Sigma Training Center
Why Choose Utah Lean Six Sigma Training Center
The Four A’s of Training
Past Clients
by Craig Johnson | Mar 16, 2021 | Education
(Cover image credit: educegroup.com)
Is Virtual Training Here to Stay?
Finding Gratitude in Tough Times
We have a tradition in my home. Every evening at the end of the day the four of us express gratitude for one thing that we experienced that day. Often that conversation is relatively easy and the gratitude is easy to come by. But sometimes it is not. Some days are, well, we’ll say… challenging… to find something for which to be grateful.
For many, the entire year 2020 was one of those days. But just like those not-so-good days, there are things we can be grateful for from the past year. One of the things for which I am very grateful is the advent of virtual training.
Sometimes Our Perception Needs to Change
If you would have asked me a year ago I would have told you in very clear terms that the classes taught at Utah Lean Six Sigma Training Center absolutely could not be taught virtually. How in the world could I possible convert twenty eight team breakout activities into a virtual environment?!
Well, turns out it really wasn’t that bad. And the virtual solution we implemented is actually pretty good! Not only is it an effective platform, but there are some distinct advantages. Students learn the concepts, but also learn methods by which they can use the concepts in a virtual environment in their own business.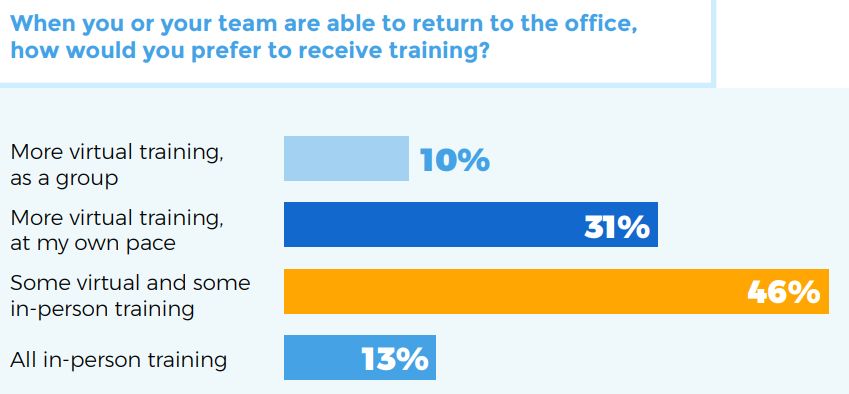
In a recent study by Kahoot, 46% of respondents said learning and development is more important than ever since the shift to remote working. Furthermore, 46% of respondents said they preferred training to continue to be a combination of virtual and in-person.
“The most popular preference for training is a blended learning system, with nearly 1 in 2 professionals saying they would prefer a mix of in-person and virtual training once they can be together at the office.”
My own experience has largely been the same. The level of learning in a virtual environment has been every bit as good as an in-person environment. The bonus of the virtual environment is that students are learning what is being taught, but also learning how they can effectively facilitate a virtual working group.
For example, in the Utah Lean Six Sigma Training Center Green Belt class, we have a team breakout session to practice effective brainstorming. When we teach in-person, groups stand together with Post-It notes in hand. In a virtual environment, students go into a Zoom breakout room and use the sticky notes tool in Lucidchart. (Side note: if you haven’t checked out Lucidchart already, do it. Now.) By doing so, the students learn how to effectively brainstorm, but they also know how to effectively use a free online tool so that they can virtually collaborate with their colleagues.
Virtual Training in 2021 and Beyond
At Utah Lean Six Sigma Training Center we remain dedicated to becoming the premier Lean Six Sigma training provider in Utah. We are passionate about providing training that is applicable to Utah industries, available in a variety of locations, formats, and schedules, attainable in a reasonable amount of time, and affordable for individuals and organizations. We have developed a robust live online format of instruction that dozens of students have successfully completed.
While I do believe that in-person training remains very desirable, I also believe that blended live/virtual training is absolutely here to stay and may even be the ideal solution. The world has shown that not only can we do it, but we can do it very well.
by Craig Johnson | Jan 13, 2021 | Education
“What would this look like if it were easy?”
-Tim Ferris
Sometimes I sit in my simple little commuter car and marvel at what a marvel of engineering it is. Thousands of intricate parts work in near perfect harmony to carry me down the road in what is the relative lap of luxury. I’m in awe of the mazes of wiring and interconnected mechanical parts. It’s stunning to me that these many complex parts and systems on top of subsystems can somehow manage to work!
In the world of continuous improvement we can find ourselves falling prey to the temptation to have intricately complex solutions to every problem. We make our forms, our systems, our processes. Controls are put in place to ensure every intricacy of our bouncing baby process is stable, repeatable, and reproducible. As a result, we find that our new process runs well, but the slightest hiccup reduces the entire thing to a smoking crater. Minor variations cause major disruptions.
I’m not going to tell you that complex solutions are bad because they’re not! Complex problems often require complex solutions. We just need to make sure solutions are applied carefully and strategically.
Because Lean Six Sigma is based on respect for our employees, colleagues, and ourselves, we need to create solutions that are as easy as possible, which is why we follow the adage to “Keep it Simple, Stupid!” or K.I.S.S.
Humor aside, it’s the first three letters of that acronym that are really important. We want to keep our solutions as simple as possible. Simplicity in design often means simplicity in implementation. Which means simplicity in practice. Which means effort and expense is low so that labor and money can be spent elsewhere.
As you create new processes or revise old ones remember to ask yourself, “How can I make this simpler?” Or in the words of Tim Ferris, “What would this look like if it were easy?”
by Craig Johnson | Feb 20, 2020 | Education
Mistake Proofing
Background
Mistake proofing, also known as error proofing, is a concept that has existed longer than anyone can accurately define. Poka Yoke, the Japanese term for mistake proofing, was formally defined and systematized by Shigeo Shingo of Toyota in the 1960’s. It has become a standard for creating processes that are designed to either not be able to produce a specific defect or automatically detect and reject a specific defect. Mistake proofing has been used across industries to create efficient workspaces and to create safe environments. To be able to implement mistake proofing we need to understand the types of mistakes people can make and then be able to put countermeasures in place to prevent those mistakes.
FMEAs are great tools, but it can be very difficult to look at a process and determine what could possibly go wrong. In the same way that a fishbone (or Ishikawa) diagram helps to add structure to a root cause analysis brainstorming event, we can add structure to our mistake proofing brainstorming as well. Instead of the 6Ms of a fishbone diagram, we use 10 common types of mistakes to organize our thought process.
The 10 Common Types of Mistakes
- Forgetfulness: People forget things when they’re not concentrating
- Misunderstanding: People make mistakes when they come to a conclusion before being familiar with a situation
- Identification: People misjudge situations because the view it too quickly or without enough detail
- Amateurs: Less experienced people tend to make more mistakes than experienced people
- Willful: People ignore rules under certain circumstances
- Inadvertent: People can be absent minded and make mistakes without knowing it
- Speed: When people go too fast or too slow, or speed up or slow down, they can make mistakes
- Standards: People make mistakes when they don’t know how to perform their duties or how success is defined
- Surprise: People make mistakes when something unexpected happens and they don’t know how to deal with the situation
- Intentional: On RARE occasions, people will intentionally make mistakes in order to sub-optimize a process or cause damage
How Does Mistake Proofing Help?
Mistake proofing allows us to reduce the risk of mistakes in a variety of ways. Here are some ways you can implement mistake proofing into your processes:
- Alert people at regular intervals as a reminder
- Enforce standard work and safety requirements
- Highlight critical elements or steps
- Automatically shut down processes or equipment event of a safety concern
- Develop a robust training program
- Give new hires the knowledge, skills, and abilities they need to be effective and safe
- “Don’t practice until you get it right. Practice until you can’t get it wrong.”
- Remove the ability to make incorrect decisions
- Define and display standard work
- Add guards, rails, beams, curtains, etc. to prevent safety events
- Create digital safeguards
- Minimum length of passwords
- Force the correct type of data input (only numbers, for example)
- Create security protocols for networked devices
How To Do It
- Describe the defect – be specific
- Identify the location at which the mistake occurs
- Detail current standard procedures
- Identify potential mistakes or deviations from standards – also look at historical data
- Identify conditions that provoke mistakes
- Perform a root cause analysis to determine why the mistake occurred or may occur
- Identify type of mistake proofing device required
- Create the device, test it, and standardize the new process